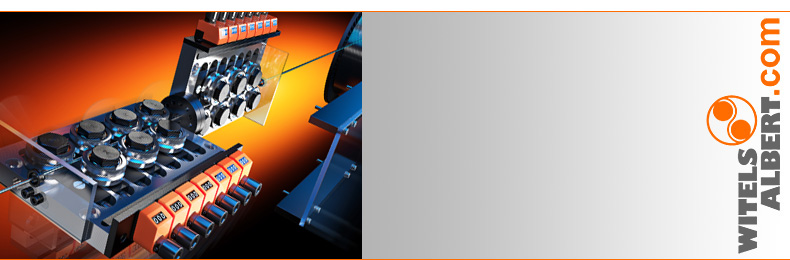
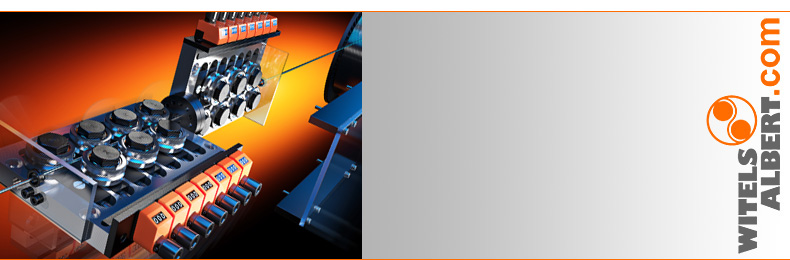
From 15. 04. to 19. 04. 2024 the WIRE 2024 will take place in Düsseldorf. WITELS-ALBERT GmbH is exhibitor at the leading trade fair of the wire, cable and rope industry and would like to inspire interested parties and customers with new products and fresh ideas. Interested parties are warmly invited to visit our stand 9 E 39 at WIRE 2024.
The effective production of electric motors means new processes, challenges and the need to work with new materials for many established manufacturers. The situation is no less complex when it comes to energy generation and supply. The green synthesis of hydrogen, the development and expansion of the infrastructure for its distribution as well as that for the distribution of electrical energy and battery cell production are all on the agenda among others.
On a smaller scale, each of these focal points has its own tasks and problems that need to be mastered and solved. WITELS-ALBERT GmbH is in demand in this context, as our understanding of processes and the resulting products support and drive forward many producers. We are proud of our products and experiences in the processing of electrical sheets and high-pressure tubes, the manufacture coated profile wires, busbars, windings, hairpins and axial flux coils, which are assigned to the processes of guiding, straightening and feeding.
Discover our eMobility solutions and products at the WIRE 2024 trade show.
Our trade show preview is available as a portfolio website on all your end devices. Scan the QR code and get an overview before the trade show begins.
For the trivial guidance of process materials with an overall geometry of less than 10 mm, the new RC 10 roller boxes are recommended, each of which represents a window for the guidance of the process material with only 2 instead of 4 guide rollers. The fully hardened guide rollers equipped with roller bearings have a specific profile which also makes it possible to significantly reduce the number of remaining individual parts. The torsion-resistant version can be mounted with 2 or 4 screws.
The uncompromising simplification of the design results in a selling price that is 60% lower than the selling price of comparable roller boxes, e.g. RK 10 and RK 10 VE. This saves the budget for the purchase and there are also advantages in terms of reducing the number of wear parts required during operation. If necessary, the roller axles and rollers can be replaced in no time at all.
The designs of these straighteners use a new PO top bar and a new design for the spindles, which serve the defined and reproducible adjustment of the grooved pieces respectively of the straightening rollers. The new design principle offers many advantages. Fewer individual parts are required for each unit, the adjustment spindles are not affected by pin bores and time is saved when mounting the straightening units. For the daily routine of the defined adjustment of straightening rollers, this means time savings and a completely new level of robustness of the straightening units, especially with regard to the incorrect operation of the adjustment spindles.
The WITELS-ALBERT GmbH roller boxes RK 20 and RK 30 are made of the wear-resistant material 1.2436. Each roller is also fully hardened to a nominal hardness of 63 HRC. Rough environmental conditions and wire surfaces as well as ever higher process material speeds cause wear, which must be avoided as far as possible from the point of view of the efforts to permanently reduce costs. The use of alternative materials is recommended, which can be hardened up to 68 HRC. However, the disadvantage of these materials is that they are costly, which makes it possible to reduce costs only to a limited extent. Of course, ceramics and tungsten carbide can also be considered, but the prices of these materials are much higher. From our point of view, these materials do not represent a solution for the economical production of solid roller bodies for roller guides.
Nevertheless, how can the service life be increased?
This is achieved by a design that uses a high-quality material such as tungsten carbide in a special geometry, which can be produced inexpensively and is available at a reasonable price.
The roller designs of the newly developed roller guides RK HM series use tungsten carbide bars placed over the roll circumference. The bars are supported by a rotation-symmetrical design element, which also houses the bearings of a guide roller and the axel studs.
Due to the gaps between the individual bars, the effect of the automatic proportional descaling of the process material results when guiding wire rod.
Nevertheless, if the tungsten carbide bars installed in the contact area with the wire are worn out after some time, they do not have to be replaced. A simple turn around the longitudinal axis by 90° increases the service life significantly. The disassembly and assembly required for this purpose can be carried out quickly and easily within the scope of maintenance.
Roller boxes of the RK and RK VE series have been part of the product range of the WITELS-ALBERT GmbH for decades.
The robust designs are used to stabilize the path of process materials in a defined horizontal and vertical direction. Due to the permanent contact of the process material, wear and tear often only occurs in a very small area on the rollers, especially if the guide gap is set close to the process material diameter. Usually only 25% of the roll length is damaged. In order to avoid damage to the process material, standard maintenance strategies recommend replacing only locally damaged rollers. Although this is good for the final product quality, it has a detrimental effect on the cost-effectiveness of the production.
Roller guides of the new RK VE SH series provide a solution to this problem, as they permit both radial and axial displacement and securing of the individually positioned rollers.
The radial adjustment and securing of the roller axels with the rollers is achieved by means of slotted holes in the basic body of a roller box and associated hexagon nuts. This is known from the RK VE series.
Due to the special design of the roller axels, axial displacement of the roller axels with the rollers is also possible. The multi-part and externally threaded roller axels protrude more or less laterally from the basic body of a roller box section after axial displacement. This may take some getting used to, but it gives users the advantage of setting the contact or wear point correctly and achieving a 4 times longer roller life.
Roller guides of the RK VE SH series are available in two sizes for process material diameters up to 5.0 mm and 10.0 mm.
The WITELS-ALBERT GmbH comes up with more accessories for straighteners RT and RTS series. New in the product range are base plates, allowing the design of straightening systems or straightening chaines.
Each straightening system or each straightening chain can consist of 2, 3 or 4 straighteners. At least 2 straighteners need to have an identical roll quantity. The known connecting brackets VW are part of the design. Just follow the link for details and dimensions. Explore the accessory with the number 16.
The processing of flat wire and strip that has an increased ratio in between width and thickness can be done with the strip straighteners BKV series easily and reliable as each roll is supported with bearings on both sides. This kind of roll support allows a straightener setup with parallel and/or conical roll gaps to manage two straightening processes with just one straightener. Both, the flat and the edge bow straightening process of flat materials can be realized with just one BKV unit.
More and more thinner and wider flat wires and strips having also increased yield points have to be straightened. For processing such materials seven straightening rolls can't be recommended anymore, as the material quality and the small thickness require a higher roll quantity for producing a perfect straightness. The new developed BKV 9-60 strip straighteners manage straightening applications with nine straightening rolls having a diameter of 16 mm only. Certainly the roll spacing is decreased as well, which allows the successfully processing of strip thicknesses in between 0.1 mm and 0.6 mm by alternating elasto-plastic bending operations.
Find our animated product presentation with all the details of the new straighteners BKV 7 and BKV 9 series. Dive in and use the information for increasing your profit.
With straightening rolls separately adjustable and supported by mechanical position displays PO, the roll adjustments on the company’s straightening machines RA H PO series becomes really easy and can be done in a short time.WITELS-ALBERT GmbH of Berlin, Germany, the world’s leading supplier of guides, feeders and straighteners for endless material comes up with several new product series for processing larger sized wire. The main focus of the new products is to minimize the amount of time and manual work needed in relation to wire infeed and straightening processes.
Help is at hand by using straightening machines RA H PO series, equipped with hydraulic cylinders for the quick opening and closing.
The elastic-plastic deformation of larger sized wire by straightening causes high straightening and transport forces, which can be calculated by the company’s process simulation program. Straightening forces of more than 100 kN per single straightening roll and transport forces of more than 10 kN are more and more common and can’t be handled manually by an operator anymore.
While offering all these features with one design for the first time, the RA H PO units define a new industry standard. The new straightening machines are recommended for a total wire size range of 9 mm to 40 mm and are available with five, seven or nine rolls.
Find our animated product presentation with all the details of the new straightening machines RA H PO series. Dive in and use the information for increasing your profit.
Humans have been using tools for thousands of years. Hammers have traditionally been used, for example, to straighten crooked nails. But that can also be quite painful! And so, in an age when powerful machines are used to manufacture nails, we’re only too happy to set the old tools aside in favour of an affordable new product for straightening process materials.
The elastic-plastic deformation of long process material sections or long goods is often necessary at various types of construction sites. In place of the simple hammer, the use of handheld straighteners is recommended. These supply the force and torque required to straighten the process material in a through-feed process, without changing the material’s cross-sectional geometry. It doesn’t matter whether the tool or the workpiece is fixed in place. The form curve of the process material changes over the length if there is a relative movement between the tool and the workpiece and the straightening rollers are positioned relative to one another. The benefits of a through-feed method compared with discontinuous straightening by means of three-point bending are improved manufacturing quality and higher throughput.
Performance density and easy handling
When designing its handheld straighteners, Witels-Albert always insists on performance density. In other words, high levels of in-process force and torsion can be achieved using straighteners with dimensions and masses that are small enough to ensure easy handling.
For this reason, almost all of the individual parts in these handheld straighteners are made from a tough non-ferrous alloy rather than steel. This alloy has a density that is two-thirds lower than that of steel, while also offering the additional benefit of being more resistant to corrosion. And the remaining parts of the handheld straightener also won’t succumb to this chemical reaction because they are made from high-quality stainless steel materials. On request, the same material can also be used to manufacture the straightening rollers, which come with a radius groove as standard. The rollers in each of the two rows on the straightener are screwed into position on separate planes, which can be moved centrically towards or away from each other.
The handheld straighteners are so well adapted to the rough conditions that prevail at construction sites that they are a pleasure to use, all the more so because additional features such as the quick-closing/quick-opening mechanism and the robust handles make the job of continuous manual straightening much easier. Handheld straighteners in the “SR” range are available in two sizes that can be equipped with five or seven straightening rollers. The models in the SPR 5 and SPR 7 ranges cover a total diameter range of 3 mm to 13 mm.
The following links will guide you to the PDF product specification sheets:
The design of a connecting bracket for connecting two straighteners RT and/or RTS series of a similar size supports the setup of 16 different straightening systems in total. Each specific straightening system uses specific versions of the straighteners RT and/or RTS series. The pages 5 and 6 of the data sheet introduce all the possibilities. It also informs about the geometrical dimensions of straightening systems, considering the straightener designs being involved and helpful accessories, e. g. mechanical position displays PO, guards or guiding blocks.
The straighteners RT series don't have a mechanism for quick opening/closing, which is installed on the straighteners RTS series. Straighteners RTS series can be opened and closed quick and easy with a small amount of force only, as a cam controlled excenter is used for the quick opening and closing. The complete new mechanism for opening and closing a straightener RTS series is very robust and reliable as it is protected against dust and dirt deposits formed from e. g. drawing soap and coating chips. In case a straightener RT series was purchased and new boundary conditions on the production frontier require a mechanism for opening and closing, it quickly can be purchased and retrofitted to build a straightener RTS series.
Both versions of the straighteners RT 5 and RT 7 series are available from stock. All the 32 different models cover a total wire size range of 0.1 - 9.0 mm. By using different straightener versions a perfect adaptation is possible, considering the wire transport direction, the location and the orientation plus the turning direction of the spool respectively of the coil. Bad straightening results by lost bending operations are history, whatever the turning direction of the coil respectively of the spool is. New materials and new standard parts, the multiple usage of single parts and a high developed assembly and production stand for the performance of the new straighteners RT 5 and RT 7 series. Here are the links to the PDF product specification sheets:
To an increasing extent, feed belts are being designed into feeding units which handle tube, cable and profiled shapes. Compared to feed rolls, they have better friction coefficients and exert less surface pressure on the work piece. At given contact pressure and torque, belts generate higher feed force than rolls. Feed belts are also gentler on the product, and they have been designed into the new NAK 60 Z feeding unit. In addition the NAK 60 Z unit features centric clamping of the process material. In contrast to upstream and downstream mechanisms, the unit can be used to clamp and feed process materials which have varying diameters or symmetrical cross-sections in thicknesses between 0.6 mm and 15.0 mm while maintaining a defined, identical zero line. (www.facebook.com/witels.albert => PORTAL => TIPS & TRICKS & NEWS).